In der Großserienfertigung, wo das Bohren durch verschiedene Materialstapel Routine ist, bietet das PKM die Präzision und Steifigkeit, die für einen sicheren, effizienten Prozess erforderlich sind. Die Möglichkeit, dieselbe Spindel sowohl zum Bohren als auch zum Beschneiden innerhalb derselben Einrichtung zu verwenden, erhöht die betriebliche Effizienz und verringert die Ausfallzeiten.
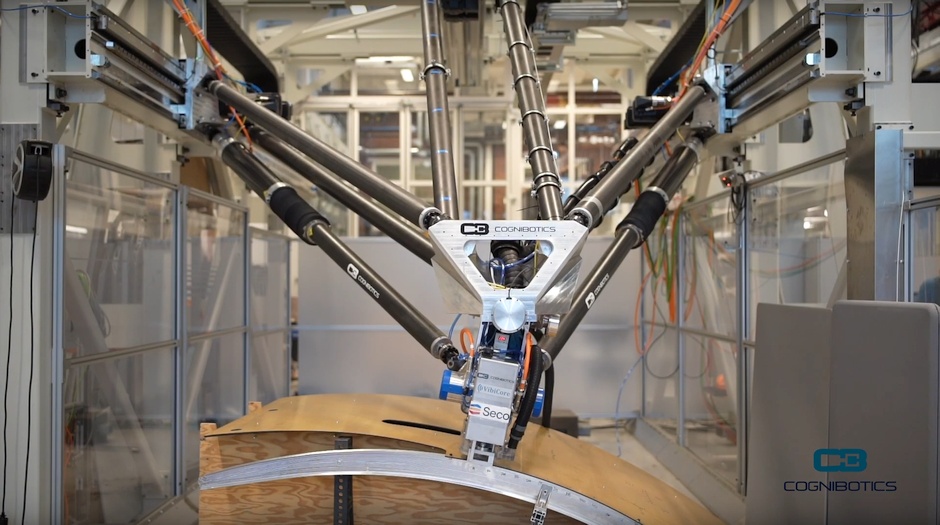
Parallelkinematik-Modul für Vibrationsbohrungen
Das PKM bietet transformative Lösungen für die Herausforderungen des Vibrationsbohrens in großen Fertigungsprojekten, wie sie beispielsweise im Luft- und Raumfahrtbau vorkommen. Das PKM zeichnet sich in diesem anspruchsvollen Umfeld durch folgende Eigenschaften aus:
● Modulares Design: Das modulare Design vom PKM ermöglicht eine einfache Konfiguration in verschiedenen Ausrichtungen und macht sie äußerst anpassungsfähig an unterschiedliche Fertigungsanforderungen und Arbeitsräume.
● Steuerung & Software: Die vollständige Integration der Spindelsteuerung mit der Maschinensteuerung sorgt für präzise Bedienung und Funktionalität, wodurch die Effizienz und Qualität der Bohrvorgänge erhöht werden.
● Nahtlose Integration: Das PKM verfügt über eine vereinfachte Spindel-Endeffektor-Einrichtung, die durch seine vollständig parallele Robotertechnologie ermöglicht wird. Diese nahtlose Integration ermöglicht eine problemlose Anpassung an verschiedene Bohranwendungen, ohne dass eine umfangreiche Neukonfiguration erforderlich ist.
● Vibrationstechnologie: Das PKM verfügt über eine fortschrittliche Vibrationstechnologie, die den Bohrprozess unterstützt. Dieser innovative Ansatz stellt sicher, dass die Späne in kleine Fragmente zerlegt werden, wodurch das Risiko von Verwicklungen, die die Qualität der Bohrung und die Effizienz des Bohrprozesses beeinträchtigen können, verringert wird.
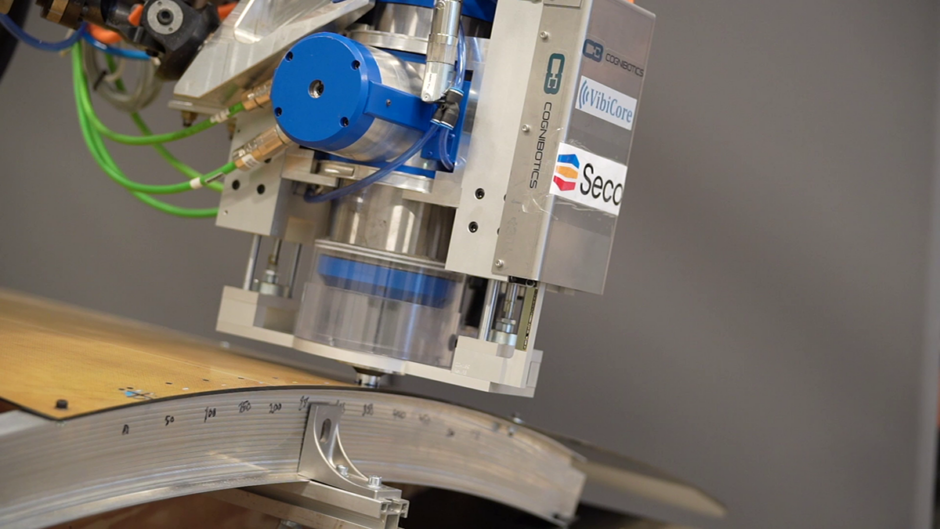
PKM mit Vibicore-Spindel und Seco-Schneidwerkzeugen
Das PKM, ausgestattet mit der VibiCore-Vibrationsspindel und Seco-Schneidwerkzeugen, bietet dem Bediener eine erweiterte Kontrolle über den Bohrprozess. In Tests hat diese Spindel optimierte NC-gesteuerte Bohrmuster gezeigt, die auf jede Materialschicht zugeschnitten sind und präzise und saubere Löcher erzeugen.
Simulation des PKM-Bohrprozesses bei Nietlöchern für Flugzeugflügel
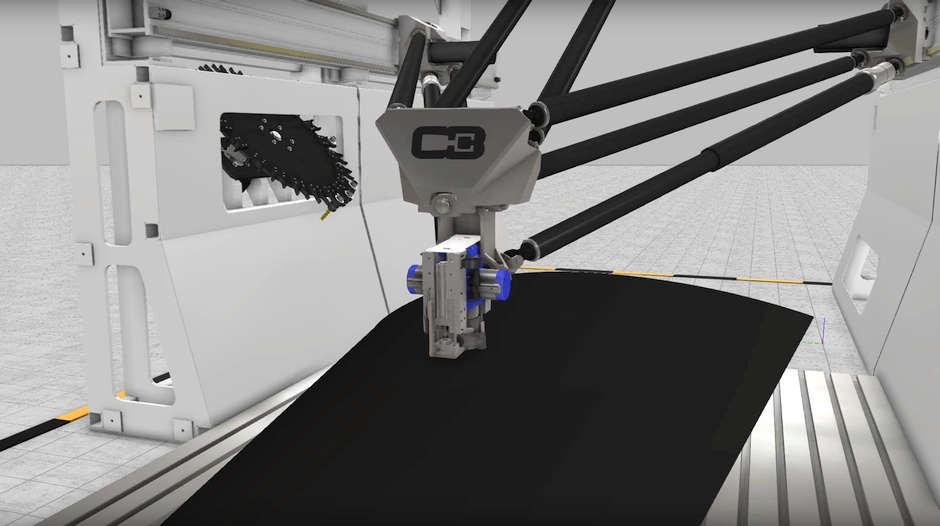
Ein kontrollierter Druckfuß hilft, die Materialschichten während der Bohrversuche zu stabilisieren, wodurch das Risiko einer Ablösung verringert und eine effiziente Entfernung scharfer Späne ermöglicht wird, was zur Erhaltung der Sauberkeit und Integrität des Werkstücks beiträgt. Der Druckfuß verfügt außerdem über einen integrierten linearen Encoder, der eine präzise Steuerung der axialen Tiefe und der Senkung ermöglicht – Ergebnisse, die eine gleichbleibend hohe Qualität der Bohrungen versprechen.
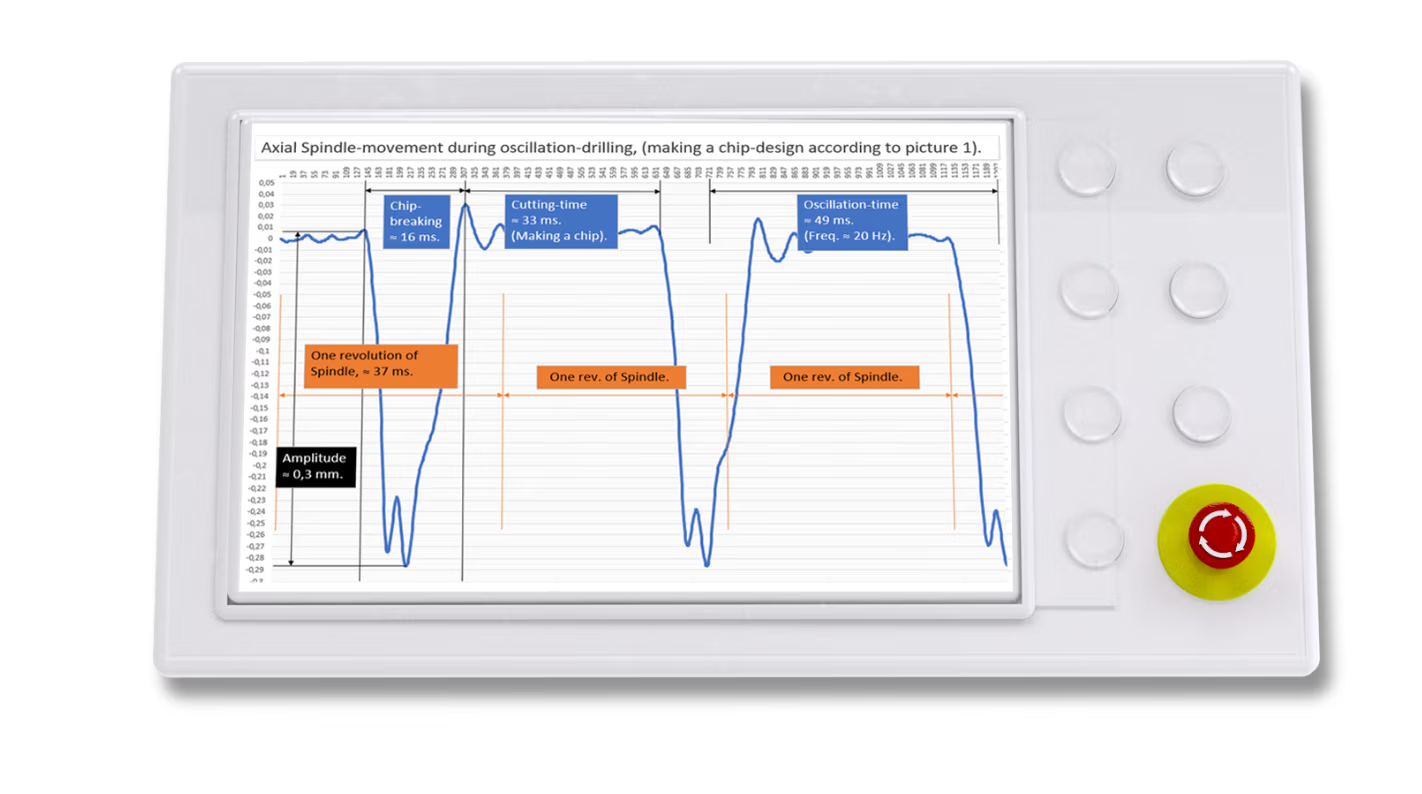
Die Oszillationsbewegung von Vibicore
Die Oszillationskurve eines typischen Vibrationsbohrens mit der Vibicore-Spindel zeigt, wie die Vibrationsbewegung mit der Vorschubbewegung des Bohrers überlagert wird. In der obigen Abbildung ist dieses Bewegungsschema erkennbar. Es unterscheidet sich von bisherigen Marktansätzen und optimiert die Schnittzeit durch eine gleichmäßige und kontrollierte Spanstärke.
Das Ergebnis: Kurze Späne und überragende Bohrergebnisse
Das Verfahren erleichtert das Trockenbohren und ermöglicht die Herstellung makelloser Löcher in einer einzigen Aufspannung, so dass keine Nachbearbeitung oder Reinigung erforderlich ist. Diese Methode unterstützt eine effiziente Einweg-Montage.
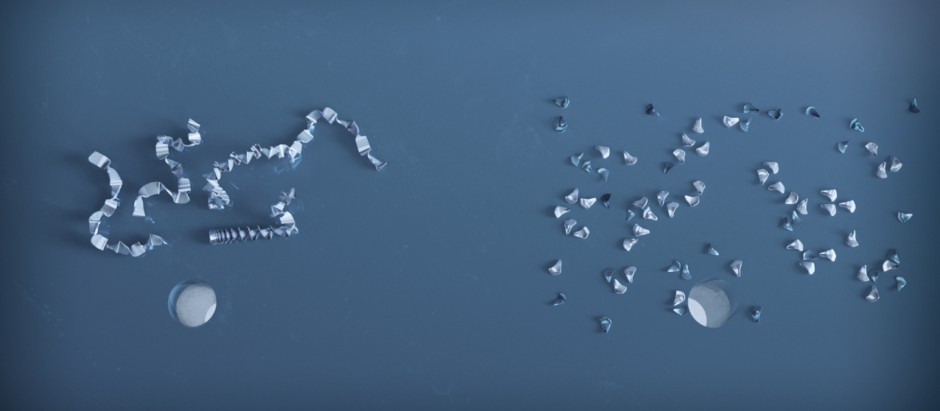
Vinnova-gefördertes Projekt: Das von Vinnova finanzierte Projekt VIBIDRILL, eine Zusammenarbeit zwischen Cognibotics, VibiCore und RISE, konzentriert sich auf die Verbesserung der Bohrpräzision und -effizienz durch fortschrittliche technologische Integration. Diese Initiative nutzt die Vibrationsbohrtechnologie von VibiCore, die mit den Robotersystemen von SigmaTau betrieben wird. Ziel des Projekts ist es, die Effektivität der robotergestützten Vibrationsbohrtechnologie zu erhöhen, um die Qualität der Bohrungen zu verbessern und die Produktionsprozesse in großen Fertigungsumgebungen zu beschleunigen. Das VIBIDRILL-Projekt zielt darauf ab, diese Technologie zu entwickeln und zu validieren, um die Anforderungen der Industrie an Präzision und Effizienz zu erfüllen.