What is the 3DMD process?
Dynamic Material Deposition (3DMD) combines powder-based laser deposition welding with the additive manufacturing of metallic components. In this process, a laser melts the material, which is then applied to a substrate. This method speeds up production, reduces energy consumption and minimises distortion.
The challenge of size in additive manufacturing
Additive manufacturing has a notable limitation: while it produces small parts with high precision, large components often lack detail and quality. The hybrid parallel kinematics module, which is equipped with a DED (Directed Energy Deposition) or a 3DMD process, addresses this problem and enables the economical production of large components without sacrificing precision.
Versatility and applications of 3DMD
Originally, the 3DMD process was mainly used for coating components. However, its ability to process different alloys and metals through a nozzle-based powder feed makes it extremely versatile. Applications include:
- Protective coatings that extend the service life of components
- Specialised surface treatments
- Reinforcement features for lightweight construction that lead to material cost savings
- Repair of components and traditional additive manufacturing
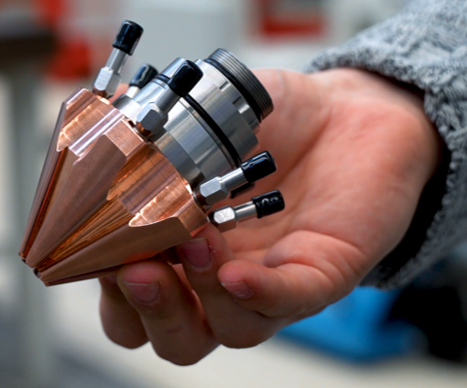
Machine specifications for optimum 3DMD performance
The implementation of the 3DMD process requires machines that enable both fast sequences and maximum precision, while also offering high rigidity and dynamic capabilities. The design of the parallel kinematics module enables high surface rates of up to 1,000 cm²/min and build volume rates of up to 600 cm³/h. It is specifically designed to maintain a constant speed in all directions and orientations to stay as close as possible to the final mould and support efficient production.
Precision manufacturing of large parts: The integration of 3DMD into the parallel kinematics module (PKM)
ELHA-MASCHINENBAU, together with Cognibotics and the technology partner Ponticon successfully integrated the dynamic material deposition (3DMD) process into the PKM. This collaboration has resulted in a versatile system that is capable of handling the production and machining of complex components made from a wide range of alloys and elementary metals.
- The hybrid parallel kinematics module handles both the production and post-processing of complex parts made of different alloys and metals in a single clamping operation. This includes:
- Additive manufacturing
- Coating
- Repair
- Post-processing and machining in the same clamping
- Large-scale productionSupports the production of large-area components within a working area of up to 3 x 2 metres in the Y x Z dimensions, with a large area in the X dimension, ensuring precise results and near-net-shape structures.
- Exceptional dynamicsAchieves maximum accelerations of 2.5 G, which significantly increases production speed and operational capabilities, especially for directional changes and contour accuracy.
- Microstructure productionCreates 3D microstructures with a minimum wall thickness of 500 μm and a surface roughness of around 20 μm.
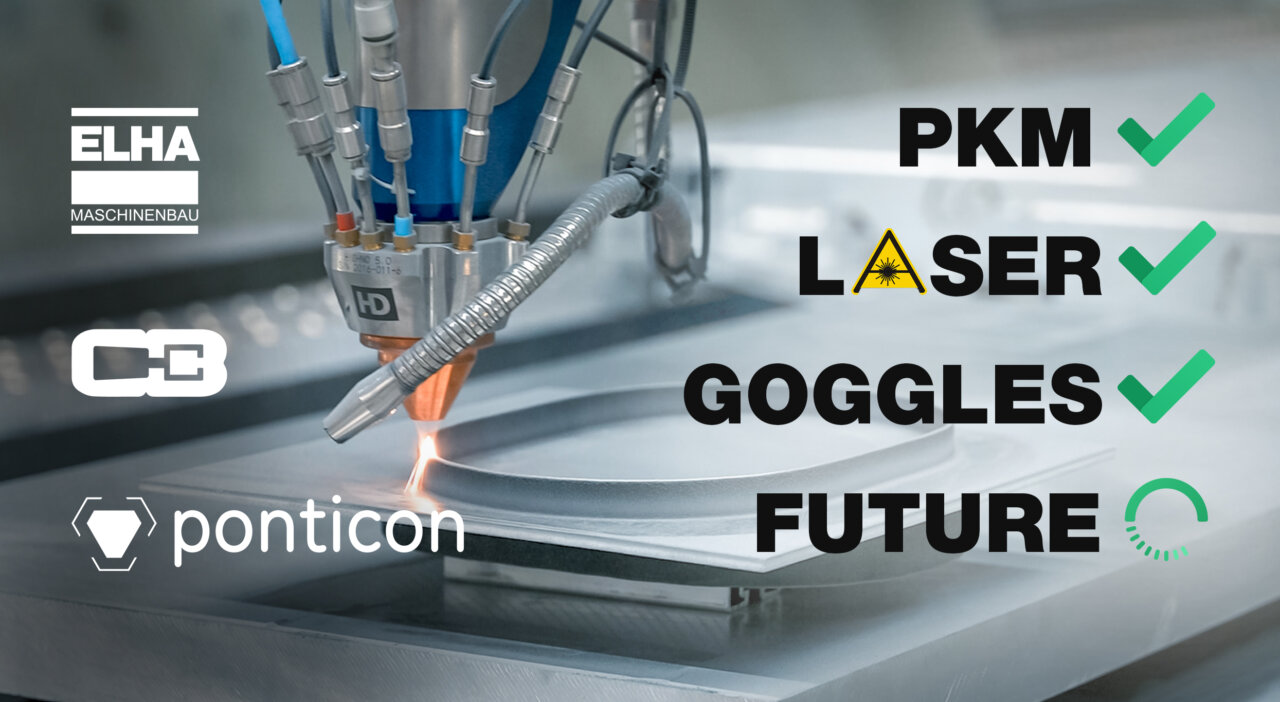
Mobile hybrid additive manufacturing as a turnkey solution
In addition, a more compact version of the PKM has been designed to fit into a standard 40-foot container and offers a working area of 1.2 x 1.2 x 2.5 metres. This design allows for easy transport and supports additive manufacturing and machining in a single facility. It offers the versatility to handle both production and repairs, whether in-house or on-site. In addition, an advanced calibration system quickly restores precision after transport, ensuring consistent accuracy in any environment.
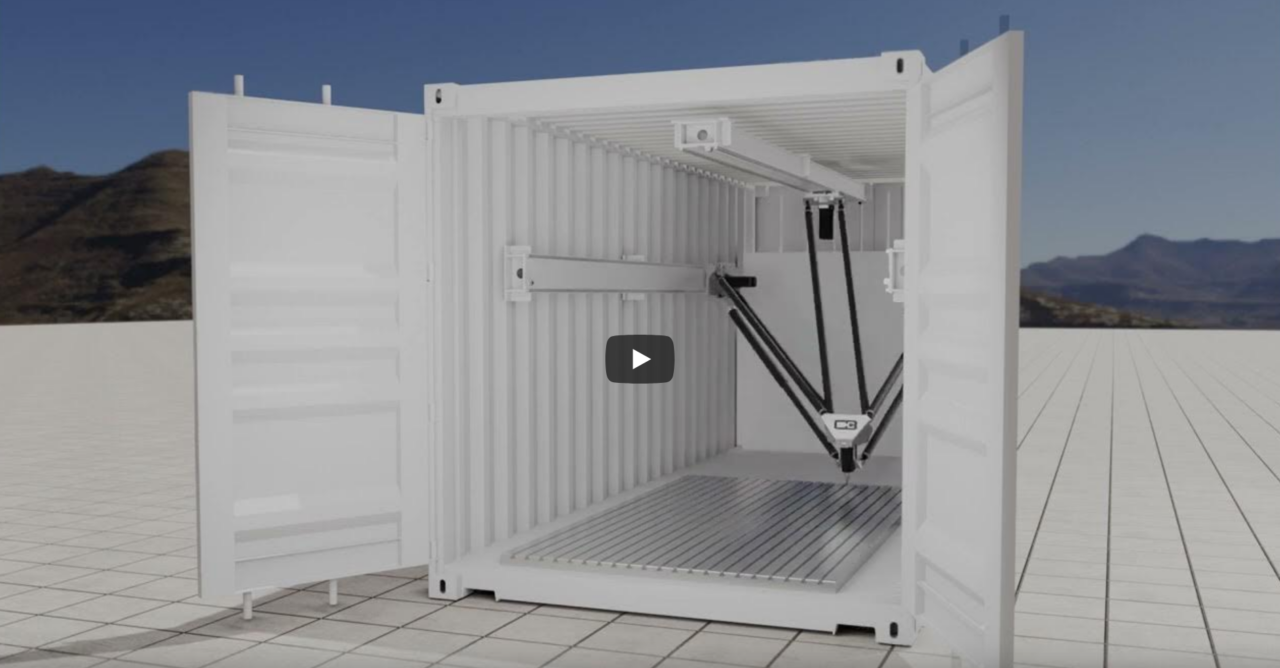
General information on the 3DMD process
In collaboration with Ponticon, we have focussed on the so-called 3DMD process, which, in combination with the parallel kinematics module, guarantees extremely fast and precise production rates. The working area of the PKM, which measures up to 4,000 x 3,000 x 2,000 mm and offers the option of 3- and 5-axis machining, opens up new dimensions for additive manufacturing.
Fast
The highly dynamic kinematics of the PKM allow for area outputs of up to 1,000 cm²/min and build rates of up to 600 cm³/h.
Precise
The highly dynamic kinematics enable area outputs of up to 1,000 cm²/min and build rates of up to 600 cm³/h.
Flexible
Combination of different alloy systems and elementary metals with nozzle-based powder feed.
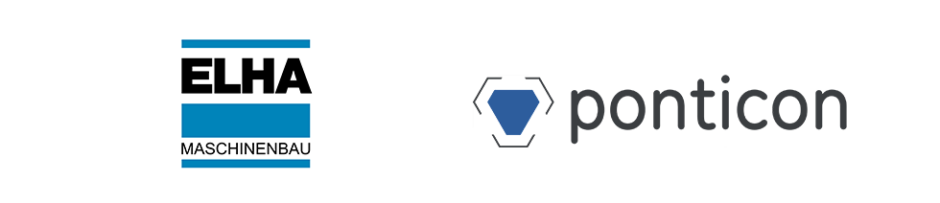
Laser cladding
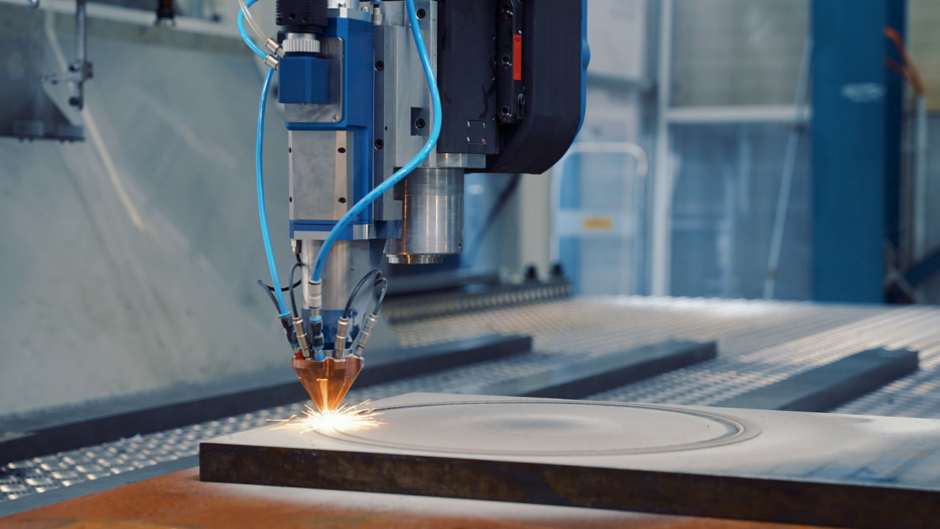
Laser Coating
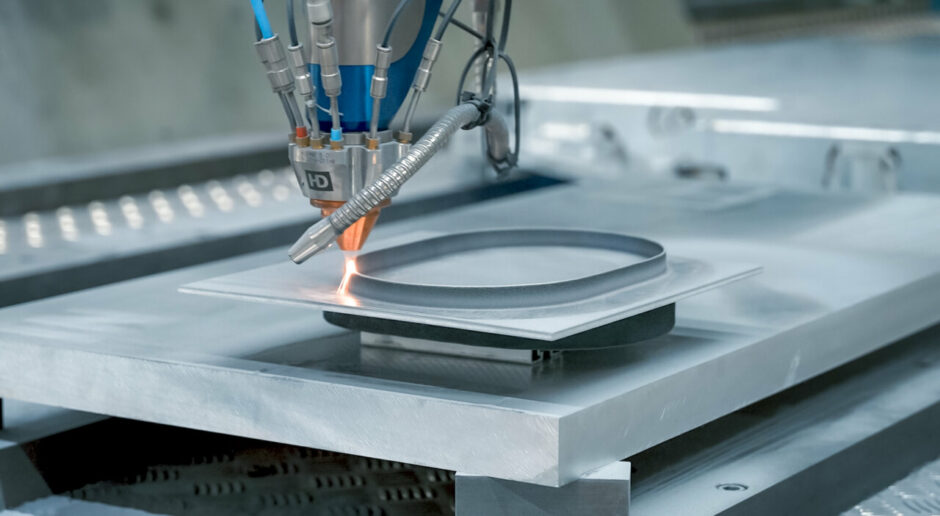
Find out more about the PKM:
Click here for the overview page
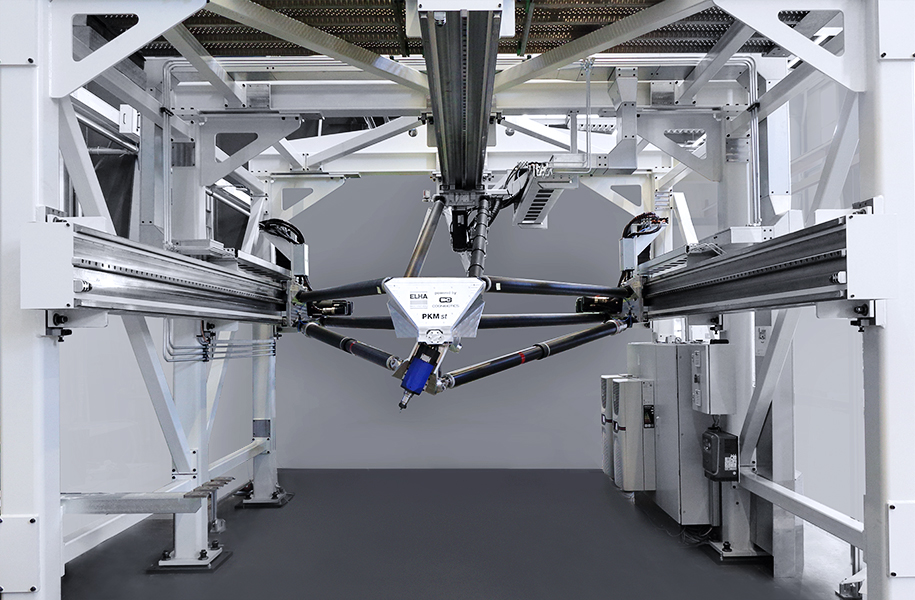
Please contact us:
Would you like to find out more about the PKM?
