Was ist das 3DMD-Verfahren?
Dynamic Material Deposition (3DMD) kombiniert pulverbasiertes Laserauftragsschweißen mit der additiven Fertigung von metallischen Komponenten. Bei diesem Verfahren schmilzt ein Laser das Material, das dann auf ein Substrat aufgebracht wird. Diese Methode beschleunigt die Produktion, verringert den Energieverbrauch und minimiert Verzug.
Die Herausforderung der Größe in der additiven Fertigung
Die additive Fertigung hat eine bemerkenswerte Einschränkung: Während sie kleine Teile mit hoher Präzision produziert, mangelt es großen Komponenten oft an Detailgenauigkeit und Qualität. Das hybride Parallelkinematik-Modul, das mit einem DED- (Directed Energy Deposition) oder einem 3DMD-Verfahren ausgestattet ist, geht dieses Problem an und ermöglicht die wirtschaftliche Herstellung großer Bauteile ohne Präzisionseinbußen.
Vielseitigkeit und Anwendungen von 3DMD
Ursprünglich wurde das 3DMD-Verfahren hauptsächlich für die Beschichtung von Komponenten eingesetzt. Seine Fähigkeit, verschiedene Legierungen und Metalle durch eine düsenbasierte Pulverzufuhr zu verarbeiten, macht es jedoch äußerst vielseitig. Zu den Anwendungen gehören:
- Schutzbeschichtungen, die die Lebensdauer von Bauteilen verlängern
- Spezialisierte Oberflächenbehandlungen
- Verstärkungsmerkmale für den Leichtbau, die zu Materialkosteneinsparungen führen
- Reparatur von Komponenten sowie traditionelle additive Fertigung
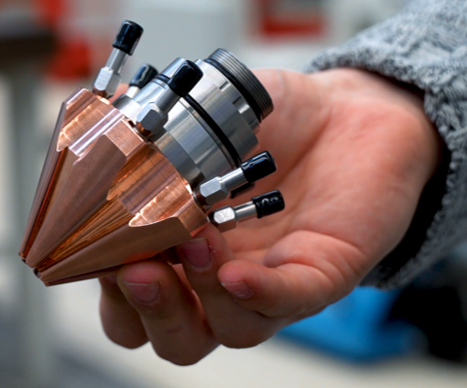
Maschinenspezifikationen für eine optimale 3DMD-Leistung
Die Implementierung des 3DMD-Verfahrens erfordert Maschinen, die sowohl schnelle Abläufe als auch höchste Präzision ermöglichen und dabei hohe Steifigkeit und dynamische Fähigkeiten aufweisen. Das Design des Parallelkinematik-Moduls ermöglicht hohe Oberflächenraten von bis zu 1.000 cm²/min und Bauvolumenraten von bis zu 600 cm³/h. Es ist speziell darauf ausgelegt, in allen Richtungen und Orientierungen eine konstante Geschwindigkeit beizubehalten, um so nah wie möglich an der Endform zu bleiben und eine effiziente Produktion zu unterstützen.
Präzisionsfertigung von großen Teilen: Die Integration von 3DMD in das Parallelkinematik-Modul (PKM)
ELHA-MASCHINENBAU hat zusammen mit Cognibotics und dem Technologiepartner Ponticon das Verfahren der dynamischen Materialabscheidung (3DMD) erfolgreich in das PKM integriert. Durch diese Zusammenarbeit ist ein vielseitiges System entstanden, das in der Lage ist, die Herstellung und zerspanende Nachbearbeitung komplizierter Bauteile aus einer Vielzahl von Legierungen und elementaren Metallen zu bewältigen.
- Das hybride Parallelkinematik-Modul übernimmt sowohl die Fertigung als auch die Nachbearbeitung von komplizierten Teilen aus verschiedenen Legierungen und Metallen in einer einzigen Aufspannung. Dies umfasst:
- Additive Fertigung
- Beschichtung
- Reparatur
- Nachbearbeitung und Bearbeitung in der gleichen Aufspannung
- Großflächige Produktion: Unterstützt die Herstellung von großflächigen Komponenten innerhalb eines Arbeitsbereichs von bis zu 3 x 2 Metern in den Dimensionen Y x Z, mit einem großen Bereich in der Dimension X, wodurch präzise Ergebnisse und nahezu netzwerkförmige Strukturen gewährleistet werden.
- Außergewöhnliche Dynamik: Erreicht maximale Beschleunigungen von 2,5 G, was die Fertigungsgeschwindigkeit und die operativen Fähigkeiten, besonders bei Richtungsänderungen und Konturtreue, erheblich steigert.
- Mikrostruktur-Fertigung: Erzeugt 3D-Mikrostrukturen mit einer Mindestwandstärke von 500 μm und einer Oberflächenrauhigkeit von etwa 20 μm.
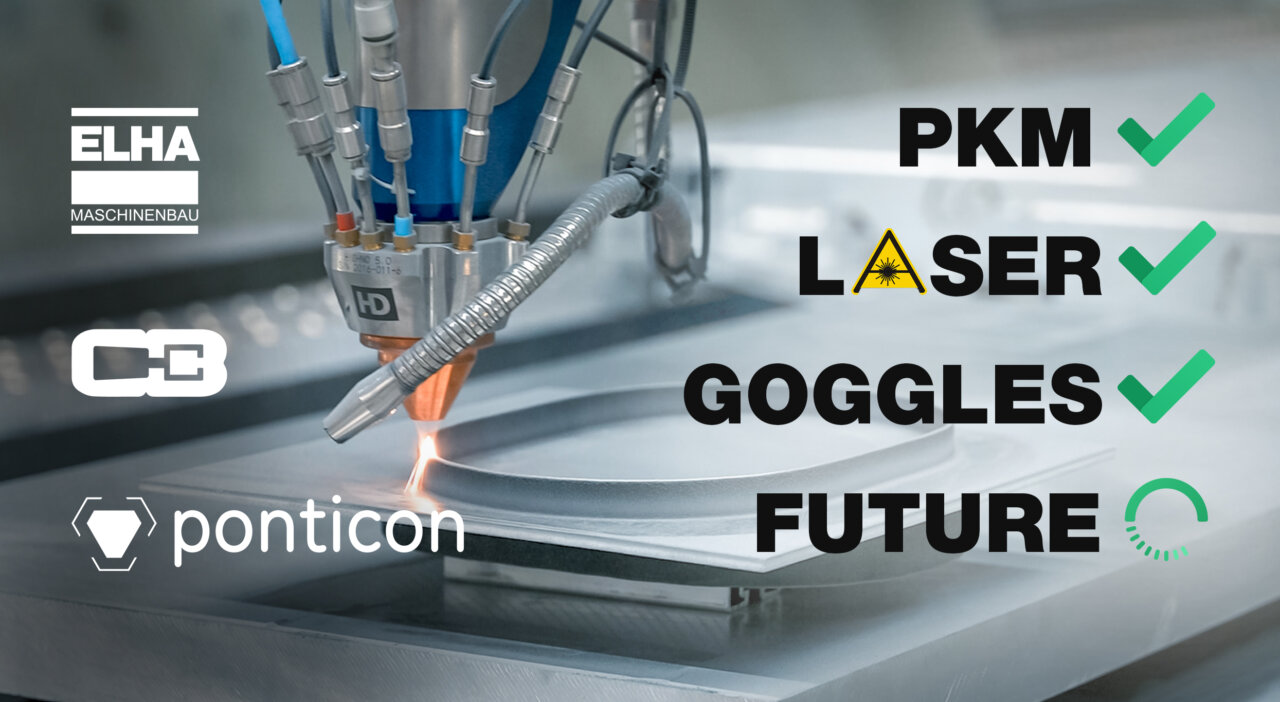
Mobile hybride additive Fertigung als schlüsselfertige Lösung
Darüber hinaus wurde eine kompaktere Variante des PKM so konstruiert, dass er in einen Standard-40-Fuß-Container passt und einen Arbeitsbereich von 1,2 x 1,2 x 2,5 Metern bietet. Dieses Design ermöglicht einen einfachen Transport und unterstützt die additive Fertigung und die maschinelle Bearbeitung in einer einzigen Einrichtung. Es bietet die Vielseitigkeit, sowohl Produktion als auch Reparaturen zu bewältigen, sei es im Haus oder vor Ort. Darüber hinaus stellt ein fortschrittliches Kalibrierungssystem die Präzision nach dem Transport schnell wieder her und sorgt für gleichbleibende Genauigkeit in jeder Umgebung.
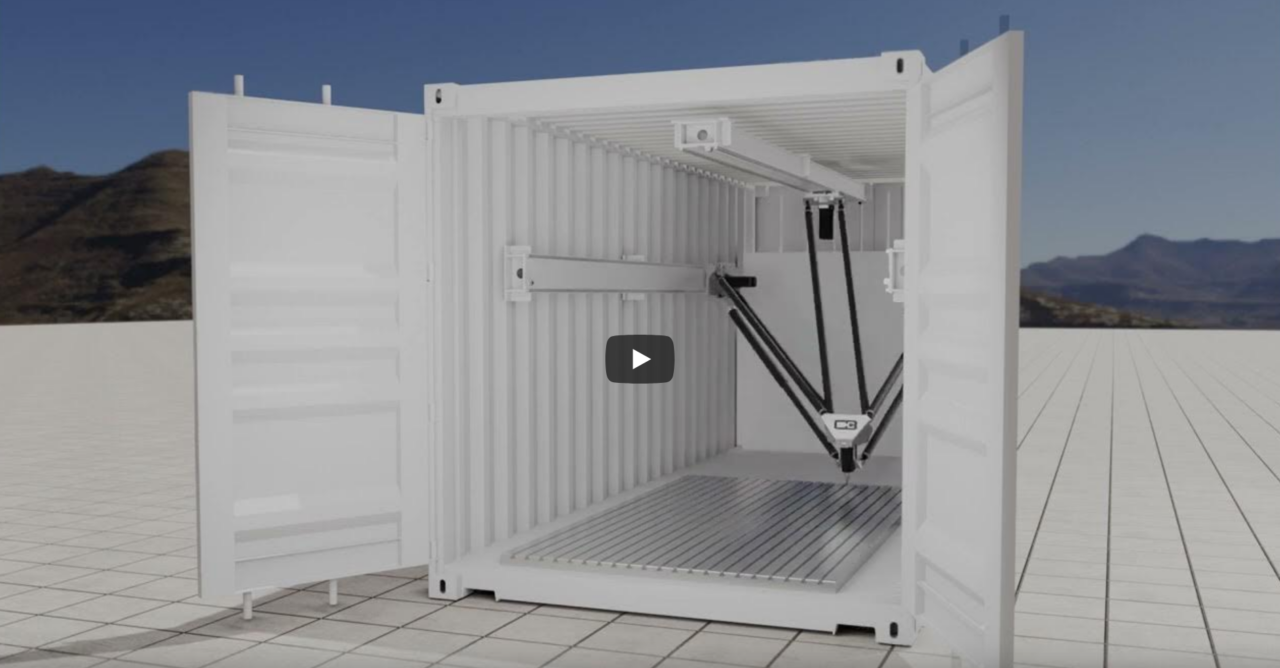
Allgemeine Infos zum 3DMD-Verfahren
In Zusammenarbeit mit Ponticon haben wir uns auf das sogenannte 3DMD-Verfahren fokussiert, das in Kombination mit dem Parallelkinematik-Modul extrem schnelle und präzise Produktionsraten garantiert. Der Arbeitsraum, der beim PKM bis zu 4.000 x 3.000 x 2.000 mm beträgt und die Möglichkeit der 3- und 5-Achs-Bearbeitung bietet, eröffnet neue Dimensionen für die additive Fertigung.
Schnell
Die hochdynamische Kinematik des PKMs ermöglicht Flächenleistungen bis zu 1.000 cm²/min und Bauraten bis zu 600 cm³/h.
Präzise
Die hochdynamische Kinematik ermöglicht Flächenleistungen bis zu 1.000 cm²/min und Bauraten bis zu 600 cm³/h.
Flexibel
Kombination verschiedener Legierungssysteme und Elementarmetalle mit düsenbasierter Pulverzufuhr.
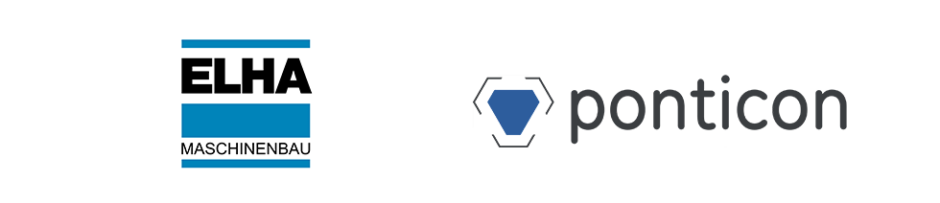
Laser Cladding
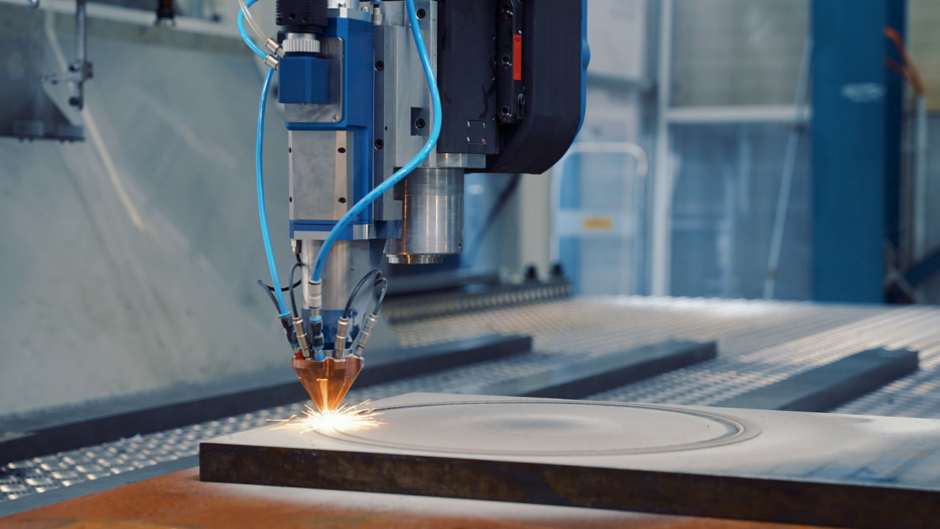
Laser Coating
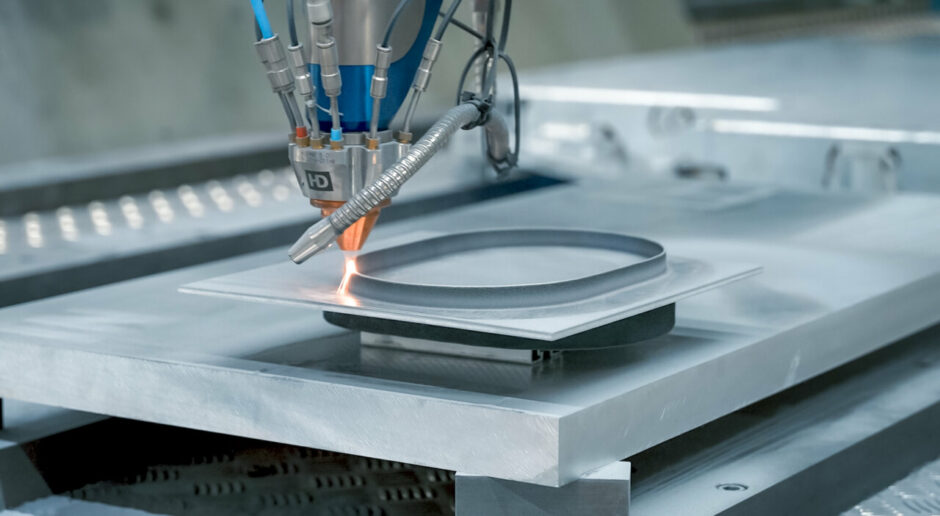
Erfahren Sie mehr zum PKM:
Hier geht’s zur Übersichtsseite
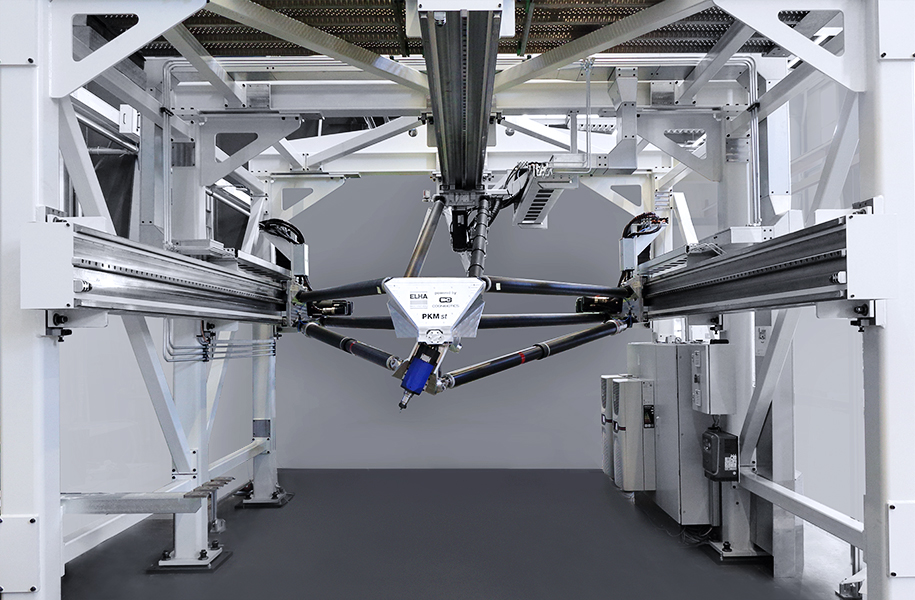
Kontaktieren Sie uns:
Sie wollen mehr über das PKM erfahren?
