The ELHA parallel kinematics module (PKM) can be equipped with almost any end effector for a wide range of manufacturing processes. Compared to a serial robot, the rigidity and accuracy of the end effector can be increased by a factor of 10 - 15. The mechanical structure of the ELHA PKM allows geometric variations of the base frame and thus the size of the working area. Compared to a large-format arm robot, the loads on the building foundation are distributed across the frame and transferred to a larger floor area. This results in maximum flexibility for the installation site, as no foundations are required.
Precision and flexibility combined
Inline machining modules from ELHA, which are built according to the PKM concept, combine the advantages of classic machine tools and flexible robot machining. A wide variety of components, including large castings, can be machined directly "inline" with unprecedented precision and flexibility. By using several modules, different machining processes such as laser cutting, milling and friction stir welding can be realised directly in one line. The modules can be mounted in any orientation of the working plane and adapted to the respective working area. Compared to a conventional robot arm manipulator, the parallel kinematic concept achieves greater accuracy and rigidity while retaining many aspects of flexibility.
Parallel kinematics as a technological bridge
Modules based on parallel kinematics close the gap between classic machine tools and conventional arm robots. The solution offers a high degree of flexibility and can be integrated into existing or new production lines. A large working area and extreme speed are the main features of the PKM. It was developed in collaboration with our partner Cognibotics.
Key facts:
The PKM is a LightweightThe arm system has a low weight, enabling maximum acceleration. Weight-optimised structures with carbon rods ensure a moving mass that is up to 20 times lower. A special feature is that the moving mass does not change when the working area is enlarged. At the same time, the PKM is easy to assemble and disassemble. The application carrier is connected to the three guide traverses via cardan joints and carbon rods. Two telescopic rods are added for full 5-axis capability. A 2-axis hv head can also be used as an alternative to the telescopic rods.
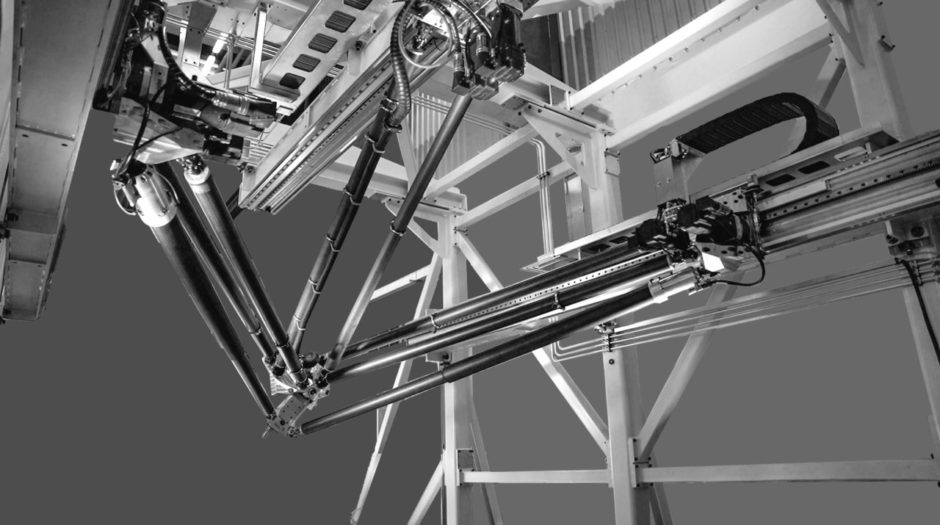
The superior rigidity achieves an accuracy ten to twenty times higher than that of serial robots, making the PKM Highly accurate. This is achieved, among other things, by using CFRP rods, which are extremely rigid in their direction of action and have a low temperature coefficient.
The parallel kinematics module also impresses with its powerful Labour. Despite the filigree structure, the available process power is on a par with that of a machine tool. The lightweight construction ensures extreme energy savings and therefore works Energy efficient. Fast and dynamic - the weight-optimised design enables extremely high dynamics. Last but not least, the PKM has the advantage of having a large workspace to offer. The linear traverse axes and the bar lengths can be flexibly adapted to the requirements.
High-performance machining solutions for large work areas can be designed and built quickly and efficiently. It is a modular system that can be easily integrated into existing production lines and simply expanded into a multi-robot machine solution. This can also be added after the initial installation.
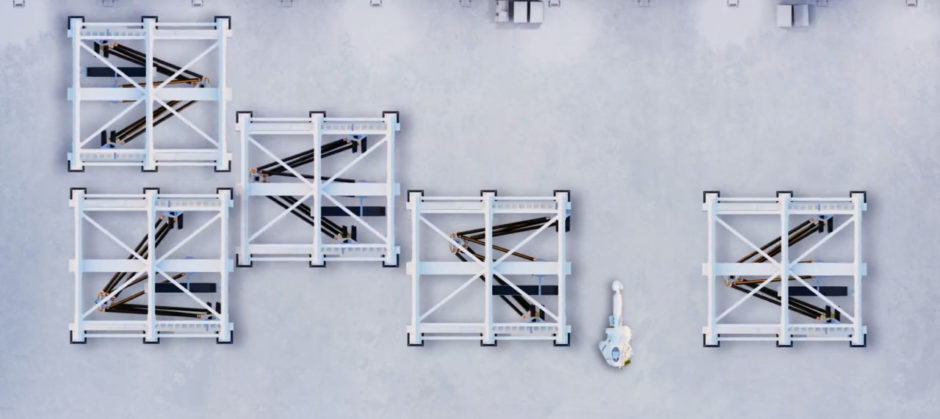
Why is the PKM just right for you?
Quite simply: the various application options and versatile configuration of the PKM. The system can be customised to suit your requirements. The high-speed configuration is optimised for low-movement masses and fast movements with a nominal acceleration of 25 m/s² and a process force of up to 6 kN. The high-force configuration is optimised for high process forces with a process force of up to 15 kN. The PKM closes the gaps between machine tools and serial arm robots - so large components are no problem.
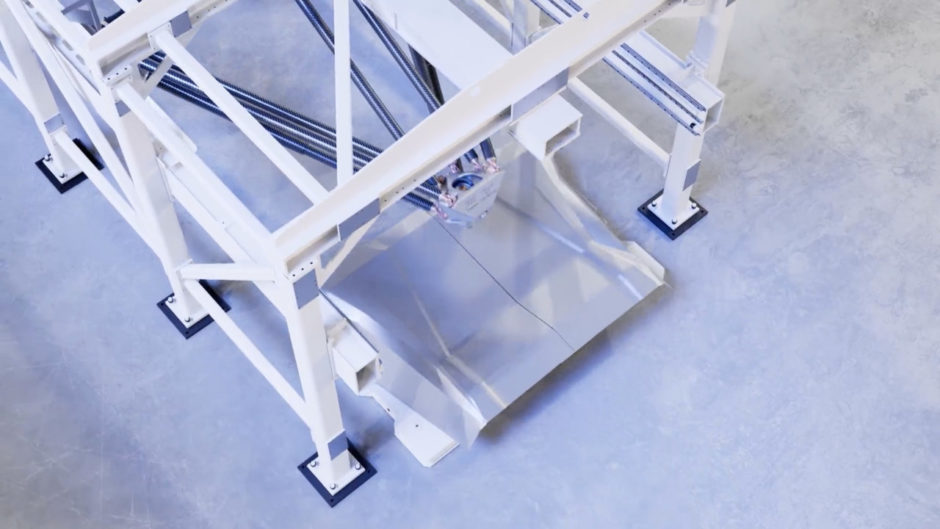
More information can be found here:
https://www.elha-robotic-automation.com/